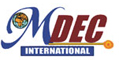
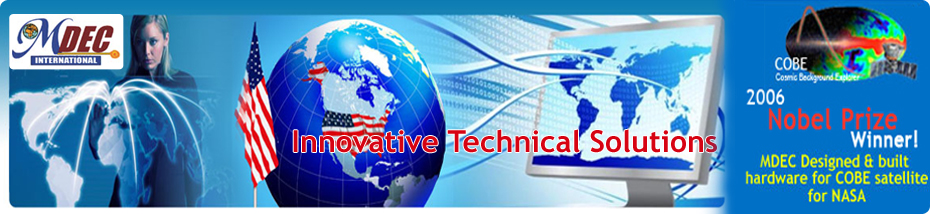

A historic Satellite
COBE (Cosmic Background Explorer), a 1 billion dollar satellite was designed and built at GSFC, Greenbelt Maryland (USA). Its primary goal was to verify Einstein’s Big Bang theory for the origin of the universe 15 billion years ago by measuring the diffused background radiation in space. (You may search the Internet with keyword “COBE Satellite” for detailed information.)
The scope of work for MDEC’s NASA projects included customer interface to analyze requirements and define product specifications, cost estimation, develop schedules and allocate resources, hardware & software analysis and design, flight hardware fabrication, QA, test & integration, technical documentation, and conducting acceptance tests to qualify flight units for satellite/Space Shuttle payloads.
AHH Project
The scope of work included the feasibility study for a small (19” dia. X 36” ht.) low earth orbit (300 n-miles) Astro Hitch Hiker (AHH) spacecraft. MDEC’s staff developed the concept to design the low power (40W average orbit power) electrical subsystems for the AHH spacecraft. The design was based on Intel’s 386 microprocessor and included Command & Data Handling subsystem, Attitude Control subsystem, power system and electrical GSE. A project management plan was also developed proposing a team of 9 engineers, programmers and technicians. The total cost estimate for the spacecraft was only 10 million dollars.
XRS Project
The scope of work for the XRS (X-Ray Spectrometer) instrument included the design of electrical power subsystem. Major responsibilities included conducting meetings with other XRS subsystem engineers & MSFC's spacecraft engineers; determine their power requirements, make presentations and resolve all power-related issues. The I/F specifications for the Power Switching & Distribution (PSD) subsystem were developed by MDEC engineers.
Our engineers defined the Power Distribution System for the X-Ray Spectrometer (XRS). We analyzed the power and interface requirements for each electronic subsystem based on parameters such as input/output voltage and current ripple, turn-on and turn-off transients, voltage regulation and efficiency. Using the 28V±7V input power, we defined the specifications for the Switching Regulators with +5V, +12V, and +24V output voltages.
EOS Project
Our engineers performed the feasibility steady and concept design of a robot for EOS (Earth Observing System) spacecraft. The design included an 8086 microprocessor controlled, battery powered, semi-autonomous robot capable of providing instrument calibration and servicing functions. We provided cost estimation for a $10 million project to design, build and lab testing of the robot.
We provided technical support to the customer for evaluating the new 120Vdc technology for EOS spacecraft electrical power system (EPS). The task included market search for qualified high voltage electrical components, searching companies that make space qualified DC/DC Converters and arranging presentations at GSFC. Established design criteria for EOS-PM S/C power system, developed a number of EPS configuration options and designed preliminary 120Vdc Regulated, 28Vdc Regulated and 28Vdc Unregulated power systems with 7KW Solar Array and 3KW load. We performed detailed technical analysis and trade studies for "120Vdc vs. 28Vdc Power Systems" and "28Vdc Regulated vs. 28Vdc Unregulated Power Systems".
GRIS Project
The project was initiated by hiring and creating a team of 10 engineers, programmers, technicians and assemblers to design and fabricate the Gamma Ray Imaging Spectrometer (GRIS) for GSFC. The 5500-pound GRIS instrument was launched using a 760 ft. diameter helium filled balloon, with the primary objective of detecting the gamma-ray sources in the outer space. The GRIS was a battery powered, 80186 microprocessor controlled instrument. We designed the hardware including the CPU & memory board, command & telemetry boards, house-keeping board, pointing system using PWM control of DC motors, power system including slow turn-on circuits, digital command I/Fs for relays and interface circuits for the GRIS-BUS.
MDEC staff designed the power distribution system for the GRIS instrument that included a 28Vdc power bus, DC/DC converters, slow turn-on circuits and digital command I/F circuits for relays. GRIS was a battery-powered instrument designed for only short (36-hour) balloon flights. The software design included an interrupt driven multi-tasking system, three-mode PID (proportional-integral-derivative) algorithm for pointing of the instrument, programmable LSI chips, command & telemetry software and diagnostic routines.
Fabrication, test and integration of all hardware/software subsystems of the GRIS instrument were done on-site at GSFC. GRIS was flown many times between 1990 and 2002. The instrument’s hardware and software worked without failure for 12+ years validating the quality of work done by MDEC team.
ISTP Project
We provided on-site electrical systems engineering support to the customer (GSFC) for SOHO instruments for NASA’s ISTP project. The three instruments involved were UVCS, MDI and LASCO. The support work included technical monitoring of the instrument provider (Ball Aerospace, Bolder, CO) to assure their compliance with the S/C requirements of schedule and allocated budgets, attending PDRs, CDRs and making recommendations to improve hardware/software designs, defining S/C to instrument electrical interfaces, writing S/C Interface Control Document (ICD), reviewing instrument Unique Interface Documents (UIDs) and resolving engineering issues such as rad-hard parts and Ground Support Equipment (GSE).
We performed a feasibility study to design a common Spacecraft Simulator for three different instruments for ISTP project at GSFC. We completed the preliminary hardware design of an IBM-PC based simulator including three interface cards for PC-AT Bus. We also designed digital circuitry to simulate S/C timing signals, parallel/serial (NRZ-L coding) telemetry data communication I/Fs and FIFO memory to store commands.
Space Station Freedom Project
We developed the Task analysis Methodology (TAM) for the Flight Tele-robotic System (FTS) for NASA’s Space Station Freedom. The TAM provided a standard method to analyze all Space Station Freedom tasks to be performed by the FTS. We developed a Natural Language as part of the TAM for the FTS to perform its tasks. We also performed a technology assessment study to utilize the FTS for Satellite Servicing System (SSS) missions.
COBE Project
We were responsible for managing the PSE (Power Supply Electronics) project for COBE (Cosmic Background Explorer) satellite. The PSE supplied 28Vdc regulated power generated by the solar arrays to COBE instruments. The task involved detailed circuit analysis of all PSE modules, thermal analysis, PC board design, packaging design, supervision of flight hardware fabrication, testing of PSE circuit boards, managing manpower and project cost to meet the budget and schedule requirements.
We designed the digital hardware for the Signal Conditioning Unit (SCU) for COBE satellite. The primary function of the SCU was to measure very low temperature (2 degree K – 4 degree K; (0 degree Kelvin = -273 degree Centigrade)) of the space background using 64 sensors, multiplex and to transmit telemetry data under command control.
We also designed the DC/DC Switching Power Converters for the Signal Conditioning unit (SCU) for COBE satellite. The converters received 28Vdc power from the PSE and converted it to +5V and +12V with full load efficiency of 84%. We supervised the fabrication of 4 converters, wrote the Qualification Procedures, debugged the prototype and 4 flight units, and conducted the Thermal Chamber testing of all the flight units.
Space Shuttle Projects
We designed the hardware for 80C86 microprocessor based MCU (Micro Control Unit) and AIA (Aviation Interface Assembly) for Special Payload of Opportunity Carrier (SPOC). The MCU contains 32 analog I/Os, 32 digital I/Os, 40 high voltage (28V) current limited outputs, 64K SRAM and 64K EPROM. The MCU was designed to provide control and data communication functions for Space Shuttle payloads. We also worked on the electrical design of the HMDA (Hitch Hiker Motorized Door Assembly) for the Get Away Special (GAS) project.
SSBUV Project
MDEC’s co-founder led a team of programmers for software design and coding of GSE application program for SSBUV satellite at GSFC. The task included analysis of telemetry data, retrieving the information from the major frame, implementing arithmetic conversions and writing the graphics display software. Code was designed, developed and debugged using MACRO-11 assembly language.
Oculometer Project
MDEC’s co-founder was responsible for developing the software for Remote Oculometer system at LRC (Langley Research Center, NASA) using FORTRAN language. The Oculometer was an infrared opto-electrical instrument that monitors and records the eye movements of the pilot in a flight simulator. The task required three dimensional graphic image processing, scientific data processing & data reduction, and development of diagnostics software.